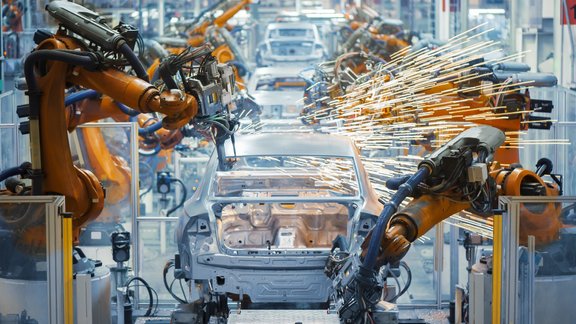
Automašīnas veiktspēja galvenokārt ir atkarīga no inženieru veikuma, taču viņiem ir jāņem vērā arī ražošanas iespējas. Ar rokām uzbūvēt iespaidīgu superauto, kurā izmantotas pēc pasūtījuma izgatavotas detaļas, nav gluži raķešu zinātne. It īpaši, ja nav nekādu ierobežojumu attiecībā uz izmaksām un laiku. Tomēr par saprātīgu summu radīt plašam patēriņam paredzētu automobili, kas ik gadu uz konveijera tiks montēts simtiem tūkstošos eksemplāru, gan ir nopietns pārbaudījums – jo īpaši tagad, pārejas periodā, kad tradicionālās degvielas segmentu pārņem elektrība.
Cik izmaksā pārveide?
Elektroauto izgatavošanas process šobrīd ir īpaši aktuāls jautājums, jo lielāko daļu savas pastāvēšanas laika autobūve ir koncentrējusies uz iekšdedzes dzinēja automobiļiem. Pāreja uz strukturāli atšķirīgo elektrisko piedziņu prasa ievērojamus ieguldījumus, jo nākas vai nu pielāgot vecās ražošanas līnijas, vai elektriskajiem modeļiem radīt jaunas līnijas, vai arī pilnībā pārveidot pašas rūpnīcas, lai tās specializētos tikai uz elektrisko transportu.
Iespaidīgas investīcijas var redzēt, piemēram, Dienvidkorejas uzņēmuma "Kia" rūpnīcā Gvangmjongā netālu no Seulas. Iepriekš tur tika izgatavotas mazas iekšdedzes automašīnas, bet tagad tā ir pilnībā pielāgota elektriskajai piedziņai. Nākamgad šeit tiks montēti arī tādi elektroauto kā "Kia EV3" un "EV4". Šādai reorganizācijai bija nepieciešami vairāk nekā 400 miljardi Korejas vonu jeb gandrīz 270 miljoni eiro. Liela daļa investīciju tika ieguldīta rūpnīcas pielāgošanā jaunākajiem ekoloģiskajiem standartiem, uzlabojot energoefektivitāti, palielinot automatizāciju un ieviešot videi saudzīgus risinājumus, piemēram, krāsas uz ūdens bāzes.
Tomēr, tā kā radikāla procesu transformācija joprojām ir ārkārtīgi dārga, ne visi ražotāji ir gatavi to darīt. Lai savu iespēju robežās pielāgotos elektrisko modeļu ražošanai, zīmoli izmanto dažādas stratēģijas. Piemēram, "Stellantis" gan elektriskos, gan iekšdedzes auto montē uz vienas līnijas. "Peugeot e-3008", kas pieejams gan elektriskajā, gan hibrīda versijā, Sošo rūpnīcā Francijā tiek ražots uz līnijām, kas paredzētas elektropiedziņai, bet pielāgotas arī hibrīdiem. Līdzīgi arī elektriskais "Ford Transit" noripo no tās pašas līnijas, no kuras tā dīzeļdzinēja ekvivalents.
Kas elektroauto ražošanā ir tik īpašs?
Portāls "Engineering.com" šīs atšķirības ir izpētījis detalizēti. Eksperti ziņo, ka iekšdedzes automobiļu līnijas var pielāgot elektriskajiem transportlīdzekļiem un pat izmantot abiem tipiem vienlaicīgi. Tomēr šāda pieeja rada problēmas, jo ražošanas process ir sarežģītāks, kā rezultātā vajag vairāk darbinieku un plašākas telpas.
Rūpniecisko iekārtu ražotājs "Stanley" savā vietnē skaidro, ka kombinētās līnijas neatbilst ilgtspējīgas attīstības principiem. Uzņēmumiem galu galā tāpat būs jāpāriet uz specializētām ražotnēm, jo tās vienkāršo ražošanas procesus un samazina izmaksas, lai gan prasa ievērojamus sākotnējos ieguldījumus.
"Elektromotoriem ir ļoti maz kustīgu detaļu. Tiem nav jāmontē izplūdes sistēma, ģenerators, degvielas iesmidzināšanas iekārta un starteris. Šādu komponentu elektriskajā piedziņā vienkārši nav. Tāpēc izgatavot to ir vienkāršāk. Plus arī – mazāk detaļu nozīmē zemākas darbaspēka izmaksas," norāda "Stanley".
Turklāt lielākā daļa elektroauto nu jau tiek būvēti uz speciālām platformām. Atšķirībā no modeļiem, kuros izmantotas pielāgotas iekšdedzes auto konstrukcijas, šie elektromobiļi ir veidoti ap lielu un smagu akumulatoru. Akumulators, kas novietots apakšā, stabilizē smaguma centru, uzlabo automašīnas stingrību un kalpo kā virsbūves strukturālā daļa.
"Ir ievērojamas atšķirības starp automobiļiem, kas radīti tikai kā elektromobiļi, un automašīnām, kas pieejamas arī ar iekšdedzes dzinēju," skaidro auto žurnālists un tehnoloģiju entuziasts Māris Gaugers. "Elektriskā piedziņa ir pilnīgi citāda, un tās galvenā sastāvdaļa ir akumulators. Parasti tas ir novietots apakšā, kas ļauj iegūt plašāku salonu nekā līdzīga izmēra benzīna automašīnās. Pat kompaktie elektromodeļi bieži vien pārsteidz ar savu praktiskumu. Tomēr ne visi tie ir veidoti pēc viena principa – dažiem ir masīva virsbūves priekšdaļa, nelīdzena grīda, plata viduskonsole, it kā tur būtu paslēpta izplūdes sistēma un pārnesumkārba. Turpretī "Tesla" savus modeļus ir projektējusi no nulles. "Model 3" priekšpuse ir īsa un zema, veidota kā ķīlis, tomēr tajā ir pieklājīga izmēra priekšējais bagāžnieks."
Agrāk vai vēlāk notiks specializācija
Kā uzsvērts "Stanley" rakstā – lai gan rūpnīcu pārbūve prasa pamatīgus ieguldījumus, izmaksas var kompensēt ar lielāku efektivitāti. Vienkāršoti ražošanas procesi, īsākas piegādes ķēdes un mazāks detaļu skaits optimizē izmaksas un paātrina darbu.
Tajā pašā rakstā citēts Herberts Dīss, "Volkswagen" vadītājs no 2018. līdz 2022. gadam. Viņš pastāstīja, ka viena "VW ID.3" montāža ilgst 30 stundas, savukārt ar "Tesla Model 3" tiek izgatavots 10 stundās. "Tesla" priekšrocība ir tā, ka visi modeļi jau sākotnēji tiek radīti kā elektroauto, kas tos padara ideālus masveida ražošanai.
Nākotnē uzņēmumiem būs jāoptimizē procesi un noteiktas rūpnīcas jāspecializē tikai uz elektromobiļiem. Tas ļaus ražot pieejamus un ietilpīgus elektroauto par pieņemamu cenu. Piemēram, "Kia" atjaunotajā Gvangmjongas rūpnīcā gadā tiks izgatavoti 150 000 elektromobiļu. Kompaktais, bet ietilpīgais "Kia EV3" ar vienu uzlādi spēs nobraukt vairāk nekā 600 km. Šī modeļa cena Eiropā sāksies no aptuveni 40 000 eiro.